Do you ever watch your OTIF improvements going backwards?
It can be disappointing to watch and it usually hurts your OTIF performance. I’m sure that you, like the rest of us, don’t want to go back to reactive working!
What can you do about this phenomena? How do you stop your business from going backwards and driving you mad?
Five approaches to consider
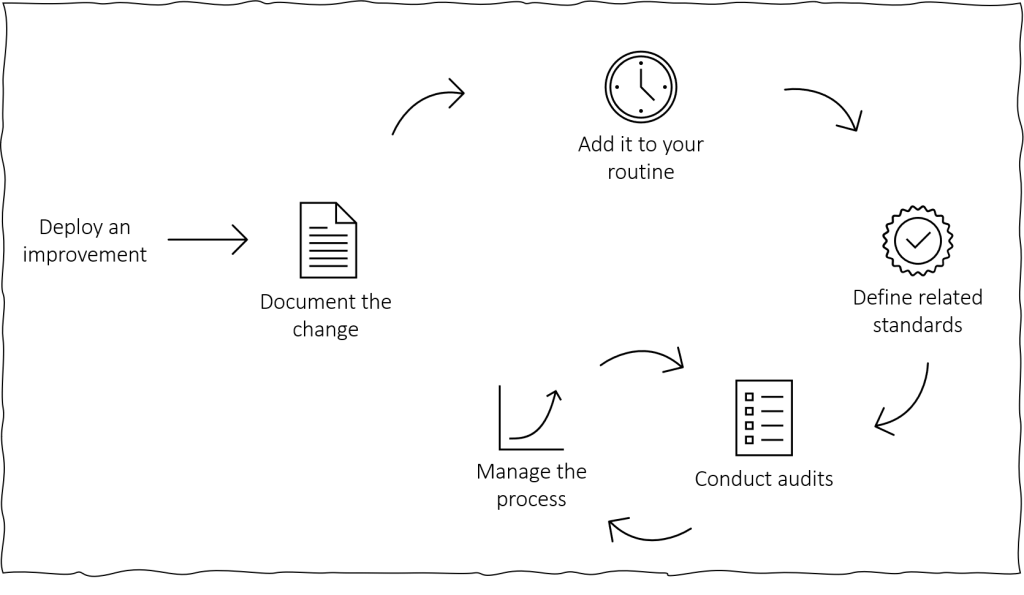
Documentation
Have you documented your processes and working practices? If you haven’t, this is a great place to start. Forgetting key steps in a process is an obvious way that improvements get lost.
You don’t need to have a long winded / encyclopaedic document, even well written notes are a good place to start. If you can tie the information into a formal management system (such as ISO 9001), even better.
Routines
Defining a routine for your teams to follow, to trigger key activities, can help stop the slide. When your team know who handles what activity and when, management simplifies.
Keeping this routine in the eye line of day to day working helps it to embed. Embedded routines become habits.
Standards
Like the documentation point, setting clear standards is essential to inform your team. If you want to maintain a certain standard, be clear about it.
The standards could be a sequence of operations, or a housekeeping standard. If it helps your business deliver on time, then capture it.
Make the standard available, and visible, which leads to the next point.
Audits
You need to check your standards often. Don’t leave auditing to be something that only the Quality Department do.
On a frequent basis, check the standards. If the standard isn’t met put an action in place to deal with it.
Little and often is the best strategy with this. Take the Kaizen approach and nibble away at reviewing your standards.
Management
My important fifth point is that you need to manage the processes you have implemented. If you see something that isn’t right you need to nip it in the bud.
We all let standards slip. It is the job of the manager to ensure that this doesn’t happen on their watch!
In summary
All improvements affect one or more processes. If you deploy the process change in the correct manner the right habits will form. These habits are stronger when accompanied with documentation, routines and standards.
Decay is a natural part of business life. Effective management and auditing can help keep this all in check.
Don’t let your OTIF performance succumb to poor management habits after your improvements have been made.