There are a few ways to deliver your projects, products or services on time.
- Poorly, raising the risk of customer dissatisfaction.
- Moderately, but not differentiating yourself from the pack.
- Well, but at huge cost (in terms of overtime, stretching your staff and ‘blood, sweat and tears’).
- Well, in a cool, calm and controlled manner.
I prefer the last option, which sounds good in a perfect world (which we definitely don’t live in currently!). However, the first three options aren’t really options, are they? They certainly aren’t a strategy that any one of us would promote.
So, how do we spend most of our time in this ‘cool, calm and controlled’ manner?
The CCC method
As with many other things in life, we need to be honest about where we are at this point in time. Specifically, we need to be honest about our management and leadership failings around this topic.
In short, if we are honest about our shortcomings creating an improvement plan becomes easier.
A great way to draw out this honest view can be done by using the Concern – Cause – Countermeasure (CCC) framework. This versatile framework can be used for a wide range of improvement work, in this case we can focus it towards on time delivery performance. In short, the CCC method follows three simple steps:
- Define your concern (what isn’t working the way it should or delivering the results it is capable of doing).
- Decide what is the root cause (the fundamental issue that is causing the concern, not just the related symptoms).
- Agree on a countermeasure (the action you are going to take to deal with the root cause).
Whilst reaching the root cause issue might not be the easiest thing to do, it is worth the effort. Don’t just hack away at the symptoms, go for the root.
Consider these items
To help you get on your way with this journey, here are some items to consider. Read each one in turn and decide if you have any concerns about the item before you move to the next consideration.
Items to consider:
- Balancing resources against project needs
- Starting projects / jobs on time
- Scheduling of the supply chain (services / materials)
- Managing the supply chain (to deliver on time)
- Monitoring progress
- Correcting progress when it slips
- Making good decisions in a timely manner (that keep ‘production’ going)
To make your life easier whilst completing this exercise, you can download a CCC template by following this link.
Once you have ‘confessed’ your shortcomings you can follow the rest of the process and think about why that situation exists. Hopefully you will get to a root cause if you keep digging.
Creating an action plan
From here the action plan should drop out. If you have done a good job of reflecting on the above questions (and any others that you think of related to on time delivery shortcomings) then you should see a jump in your performance. If you have done a really good job then some of the irritations you face on a daily basis will dissolve completely.
This is not necessarily easier said than done, but usually doesn’t happen without some effort. Don’t forget that you can revisit these questions and this method as often as you want. Starting small and having many attempts at this topic is a really good approach.
If you want some additional help, then don’t forget to check out the resources listed below.
Good luck with your reflection.
Effective Root Cause Analysis
If you want practical advice on how to get the most out of root cause analysis, and see how far you can take the gains from this approach, read Effective Root Cause Analysis today.
Available from Amazon.
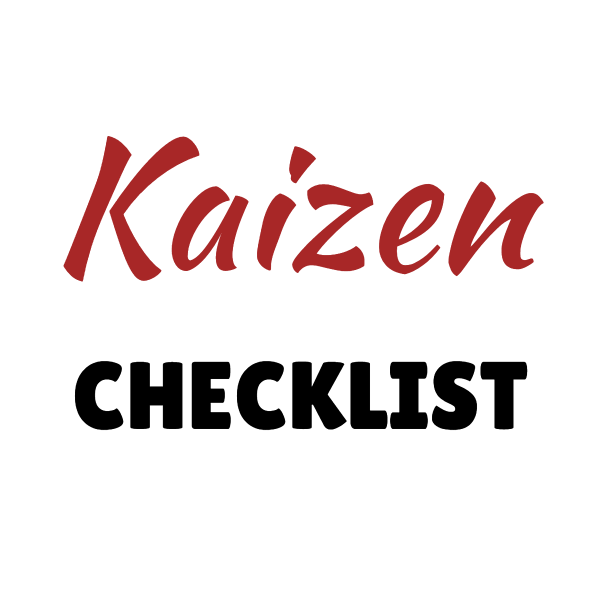
Kaizen Checklist
Harness the power of Kaizen, and avoid the pitfalls that many businesses face, with this downloadable guide and toolkit.